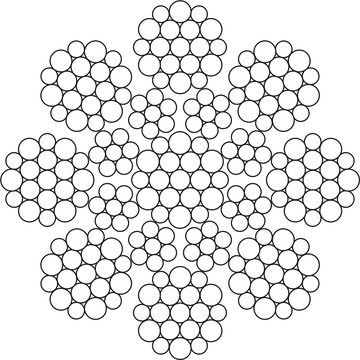
Ropes for lift and elevators
Ropes for lift and elevators are specifically designed for the safe and efficient operation.
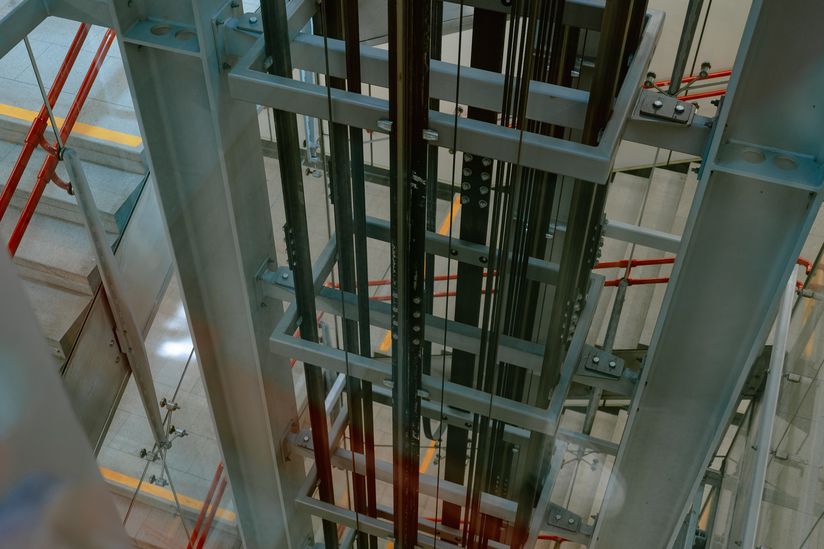
Steel strength, seamless lift
These ropes provide high tensile strength and flexibility, ensuring smooth and reliable elevator performance. They are engineered to meet stringent safety standards, making them ideal for both residential and commercial buildings.
Discover our ropes portfolio for lift and elevators
Our Services for Wire Ropes
We are able to control the entire production process for our cables, from procurement of the raw material, to drawing, to rope closing, ending with testing and inspections. Thanks to this complete production process, the in-depth know-how and skill of our technicians, and our more than a century of experience, we have the skills to design our own production machinery.
Frequently asked questions
Any Doubts? Check here
Strength and Durability: Steel wire ropes are very durable and can withstand heavy loads and harsh environmental conditions.
Flexibility: They are designed to be flexible, making it easy to maneuver when lifting.
Safety: They offer greater safety than other materials due to their construction features.
Compaction of the strands: this allows a greater distribution of the contact pressures between the rope and the grooves of the kinematics, reducing the wear of the wires of the rope strands.
Plasticization: The ropes can have an internal metal core covered with plastic extrusion (generally polypropylene), allowing the rope to work better with high deviation angles and to better withstand shock loading phenomena by limiting the leakage of the internal strands.
Diameter tolerance: A standard rope is produced with an effective diameter which, according to the EN 12385 standard on hoisting ropes, must be between 0% +5%.
To increase the life of a rope and in any case in accordance with the design tolerances indicated by the machine manufacturer, you can request a rope with a specific diameter tolerance, for example with an effective diameter of +2% +4% or +1% +3%.
Lubrication: in addition to avoiding internal and external corrosion phenomena on a rope, it reduces wear caused by friction between the wires of the internal and external strands. Relubrication during maintenance of the rope itself increases the service life.
According to Legislative Decree 81/08, steel ropes must be checked at least once every three months after installation, except for conditions of use for which it is advisable to reduce this periodicity.
Checks must be carried out by qualified and trained personnel. Specifically, technicians experienced in inspections of lifting equipment and ropes.
Nominal diameter of the rope: determined by the geometric parameters of the kinematics of the machine on which it will be installed.
·Formation: with the same diameter, a rope can be produced with various types of formation, which develop specific breaking loads and adapt to different types of application. Identifying the type of machine, the number of quickdraws and the operating range is decisive for choosing the most suitable rope for use.
Minimum breaking load of the rope: value determined by the designer and highlighted in the machine booklet
Working environment: consider whether the rope will be exposed to environmental conditions that determine its surface finish, type of grease applied and lubrication methodology.
Surface treatment: a rope can be polished, untreated raw steel wire, or galvanized; the type of galvanizing depends on the working environment where the rope will be used. Galvanizing is a surface treatment that allows steel wire rope greater resistance to corrosion in particular conditions and environments of use.
Lubrication: depending on the working environment and its particular use, a rope can be lubrication-free (DRY), or have internal and external lubrication. Lubrication on a rope can be light or heavy depending on the operating environment.
It is always advisable to consult the rope manufacturer for technical advice and ensure the correct choice of rope.
Visual inspection: Checking for obvious signs of wear, corrosion, wire breakage, or warping.
Dimensional control: measurement of the diameter and stranding pitch of the rope.
Break test: Allows you to check the actual breaking load or the residual load of a rope.
Non-destructive testing: magneto-inductive testing to identify internal defects. Tests of fundamental importance such as the internal state of the rope cannot be verified by eye.
As indicated by the UNI ISO 4309 standard on rope acceptance and rejection criteria:
Breaking of wires according to the standard rejection criteria
Significant corrosion.
Noticeable warping or twisting.
Reduction of the diameter compared to the original measurements.
The website www.teci.it
From the cable catalogue downloadable from the website
By contacting the Teci sales network or our technicians directly
Strength and Durability: Steel wire ropes are very durable and can withstand heavy loads and harsh environmental conditions.
Flexibility: They are designed to be flexible, making it easy to maneuver when lifting.
Safety: They offer greater safety than other materials due to their construction features.
Nominal diameter of the rope: determined by the geometric parameters of the kinematics of the machine on which it will be installed.
·Formation: with the same diameter, a rope can be produced with various types of formation, which develop specific breaking loads and adapt to different types of application. Identifying the type of machine, the number of quickdraws and the operating range is decisive for choosing the most suitable rope for use.
Minimum breaking load of the rope: value determined by the designer and highlighted in the machine booklet
Working environment: consider whether the rope will be exposed to environmental conditions that determine its surface finish, type of grease applied and lubrication methodology.
Surface treatment: a rope can be polished, untreated raw steel wire, or galvanized; the type of galvanizing depends on the working environment where the rope will be used. Galvanizing is a surface treatment that allows steel wire rope greater resistance to corrosion in particular conditions and environments of use.
Lubrication: depending on the working environment and its particular use, a rope can be lubrication-free (DRY), or have internal and external lubrication. Lubrication on a rope can be light or heavy depending on the operating environment.
It is always advisable to consult the rope manufacturer for technical advice and ensure the correct choice of rope.
Compaction of the strands: this allows a greater distribution of the contact pressures between the rope and the grooves of the kinematics, reducing the wear of the wires of the rope strands.
Plasticization: The ropes can have an internal metal core covered with plastic extrusion (generally polypropylene), allowing the rope to work better with high deviation angles and to better withstand shock loading phenomena by limiting the leakage of the internal strands.
Diameter tolerance: A standard rope is produced with an effective diameter which, according to the EN 12385 standard on hoisting ropes, must be between 0% +5%.
To increase the life of a rope and in any case in accordance with the design tolerances indicated by the machine manufacturer, you can request a rope with a specific diameter tolerance, for example with an effective diameter of +2% +4% or +1% +3%.
Lubrication: in addition to avoiding internal and external corrosion phenomena on a rope, it reduces wear caused by friction between the wires of the internal and external strands. Relubrication during maintenance of the rope itself increases the service life.
Visual inspection: Checking for obvious signs of wear, corrosion, wire breakage, or warping.
Dimensional control: measurement of the diameter and stranding pitch of the rope.
Break test: Allows you to check the actual breaking load or the residual load of a rope.
Non-destructive testing: magneto-inductive testing to identify internal defects. Tests of fundamental importance such as the internal state of the rope cannot be verified by eye.
According to Legislative Decree 81/08, steel ropes must be checked at least once every three months after installation, except for conditions of use for which it is advisable to reduce this periodicity.
As indicated by the UNI ISO 4309 standard on rope acceptance and rejection criteria:
Breaking of wires according to the standard rejection criteria
Significant corrosion.
Noticeable warping or twisting.
Reduction of the diameter compared to the original measurements.
Checks must be carried out by qualified and trained personnel. Specifically, technicians experienced in inspections of lifting equipment and ropes.
The website www.teci.it
From the cable catalogue downloadable from the website
By contacting the Teci sales network or our technicians directly